Resources
CAD to Cost
Why Leveraging 3D CAD Data Provides a Competitive AdvantageUnlock Competitive Advantage with 3D CAD-Driven Costing
In today’s fast-paced product development environment, companies that can quickly and accurately predict manufacturing costs gain a decisive edge over their competitors. By harnessing the power of 3D CAD models for cost estimation, you unlock new levels of speed, precision, and automation — critical advantages that drive better business outcomes.Why 3D CAD-Based Costing Achieves Both Precision and Speed
Faster Time to Insight
Traditional costing methods often rely on manual calculations or 2D drawings, slow decision-making, and introduce risk. With 3D CAD models, much of the data needed to estimate costs is already embedded within the design. This not only means you can automatically calculate cost impacts in minutes rather than days, but you can get the insights in real time, during the design process. The result is accelerated design cycles and real-time optimization.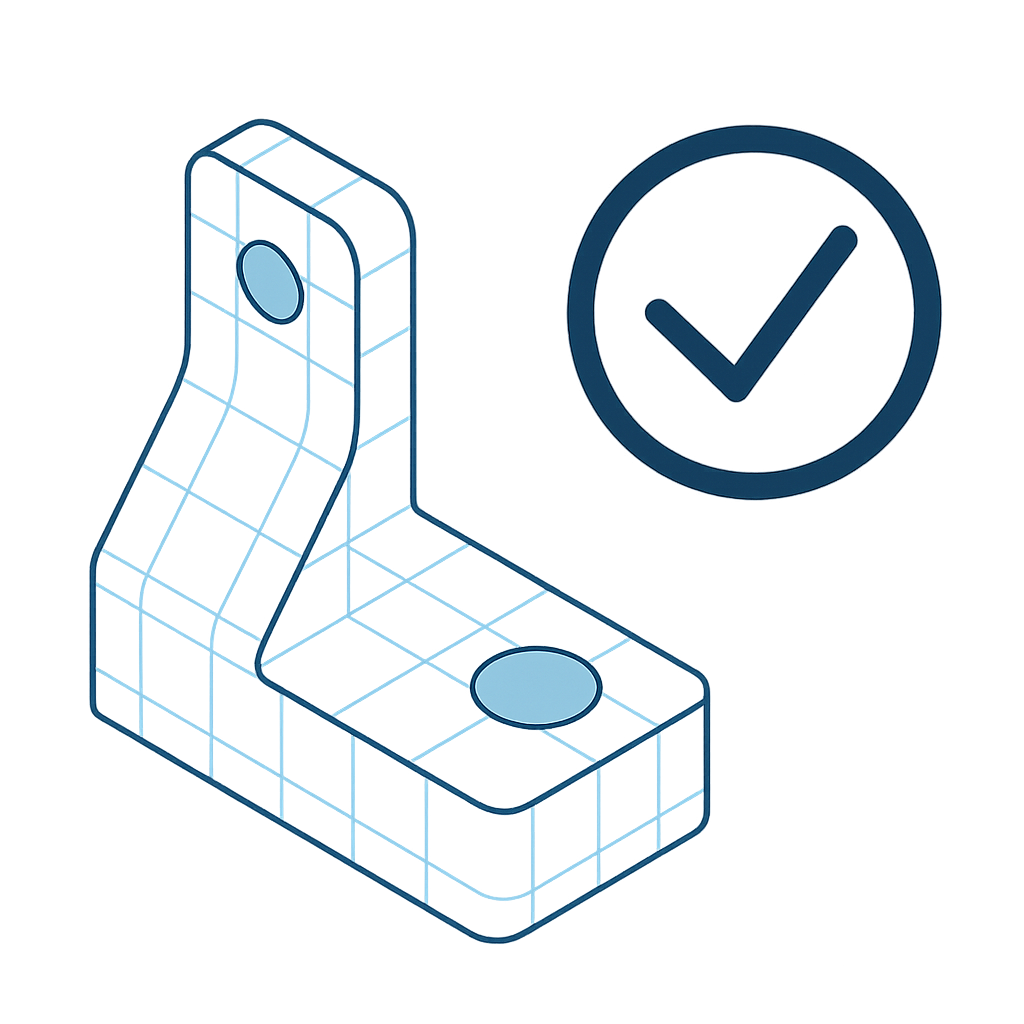
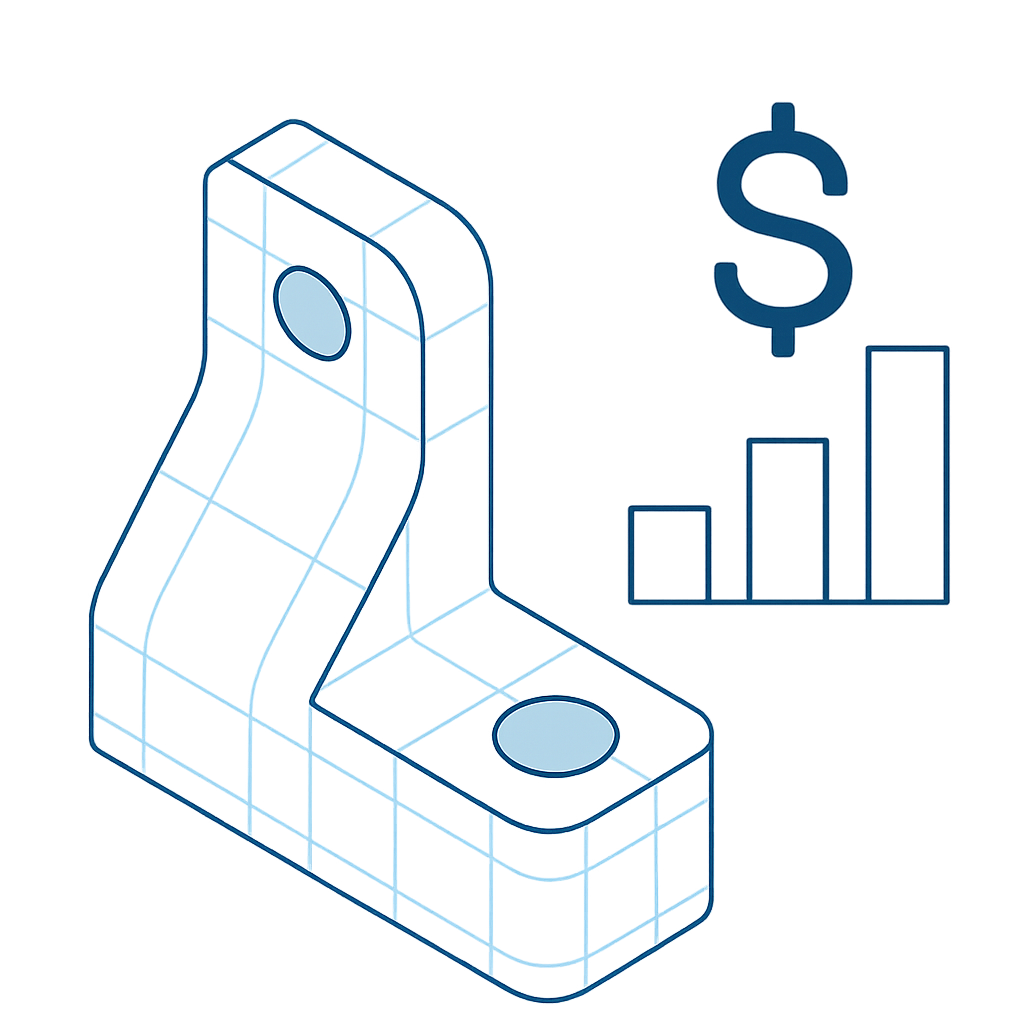
Higher Precision, Fewer Surprises
3D CAD captures a complete and accurate representation of the design, not only the geometry/shape but also metadata such as material specifications, dimensions and tolerances, and/or manufacturing processes. This precision enables more accurate cost predictions, dramatically reducing the risk of late-stage engineering changes, project cost overruns, and expensive surprises in production.Beyond a cost calculation, aPriori gives insight into what is driving the costs. A full manufacturing simulation is behind the numbers, including secondary processes, tool changes, cooling times, and the Design Guidance from aPriori gives direct feedback on how to optimize the design.
Automation and Scalability
By connecting 3D CAD models with advanced digital manufacturing simulations, companies can automate the entire cost estimation process. This not only frees up valuable engineering time but also ensures consistent, repeatable results across complex product portfolios — empowering your teams to focus on innovation rather than repetitive tasks.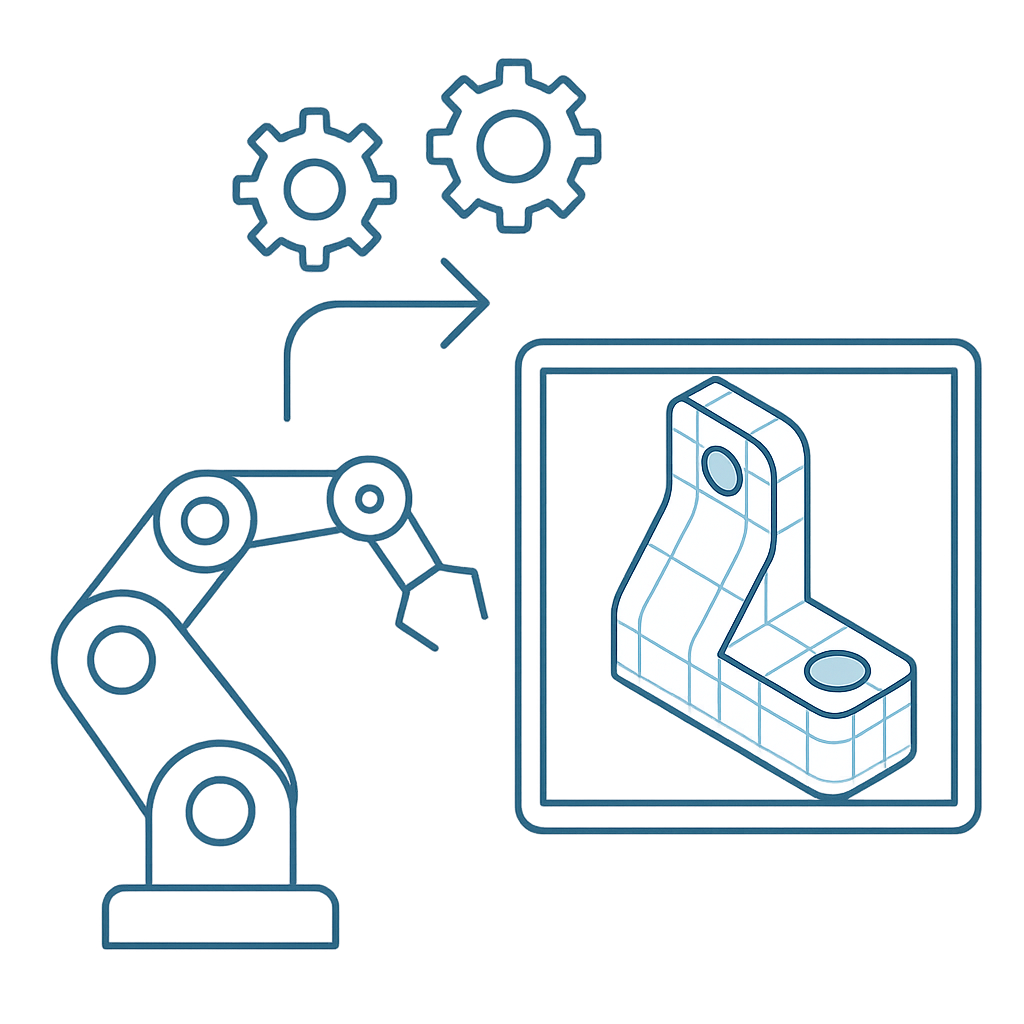
Learning from the Past:
Why 3D Replaced 2D
The shift from 2D CAD to 3D CAD fundamentally transformed product design. 2D drawings were prone to errors, missing details, and misinterpretations, leading to costly delays and rework. 3D CAD resolved these issues by providing a comprehensive digital representation of the product, dramatically improving communication, accuracy, and design efficiency.
Today, we see a similar transformation in how companies predict manufacturing costs. Just as 3D CAD superseded 2D for design clarity and quality, 3D-driven costing is now replacing outdated estimation methods, enabling smarter, faster business decisions from the very first stages of development.
Today, we see a similar transformation in how companies predict manufacturing costs. Just as 3D CAD superseded 2D for design clarity and quality, 3D-driven costing is now replacing outdated estimation methods, enabling smarter, faster business decisions from the very first stages of development.
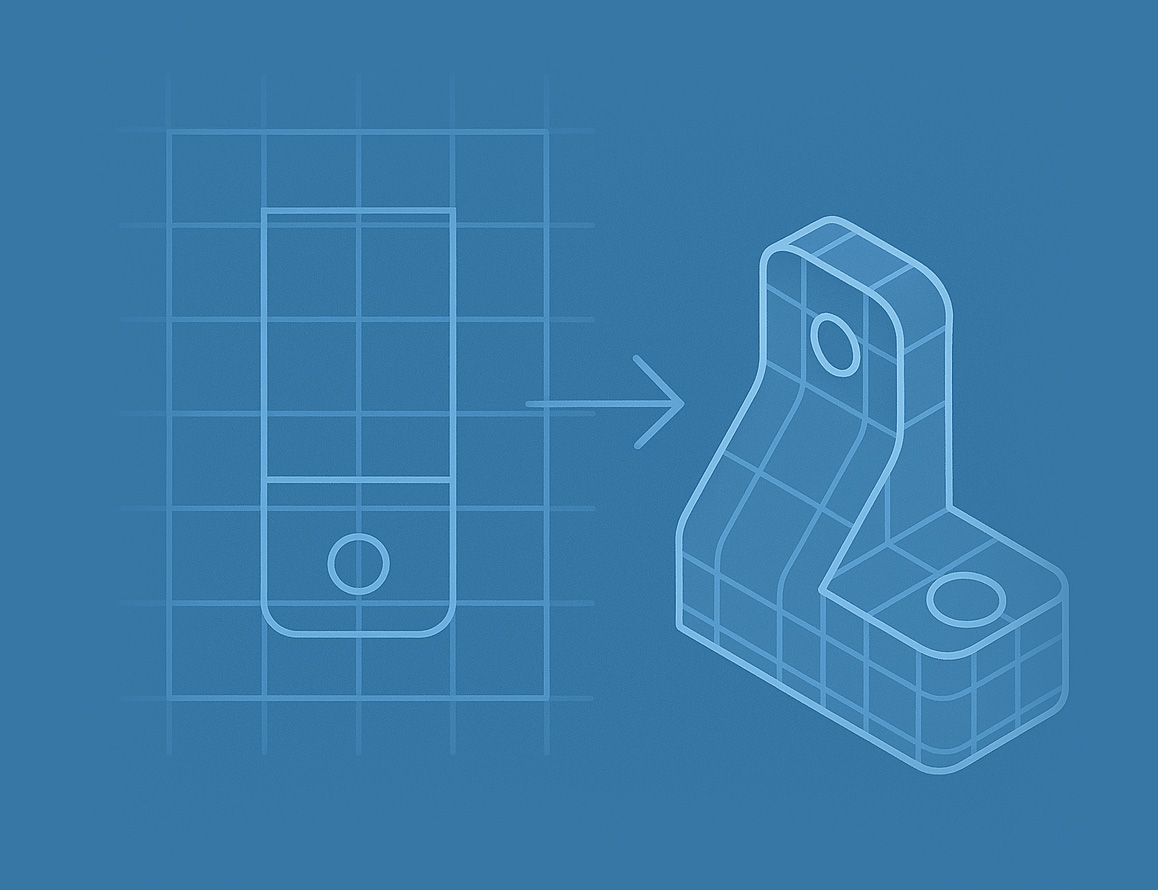