aPriori Technologies
Transforming the Manufacturing Industry Since 2003“aPriori is disrupting the industry’s status quo”
Founded in 2003, aPriori is disrupting the industry’s status quo with groundbreaking work helping manufacturers digitally transform their businesses. Through our unique, patented, intellectual property, we enable manufacturers to accelerate product design, and bring products to markets faster while providing visibility to the sustainability of their design and manufacturing choices. Our impact is profound - our customers save millions of dollars each year, accelerate time to market, all while creating a better world for future generations. Though we are an established software firm, through our continued growth, we have maintained the dynamic, collaborative nature of a start-up.
With a global presence, including North America, Europe, Asia, and India, we encourage an inclusive work environment and support employees’ growth through education, training, wellness, and other programs. As our greatest asset, employees’ contributions are acknowledged through monthly company-wide meetings, often with promotions and awards. We promote a positive work culture, employee-friendly policies, flexible work schedules, pub nights, and an additional day off each quarter known as “aPriori Day”.
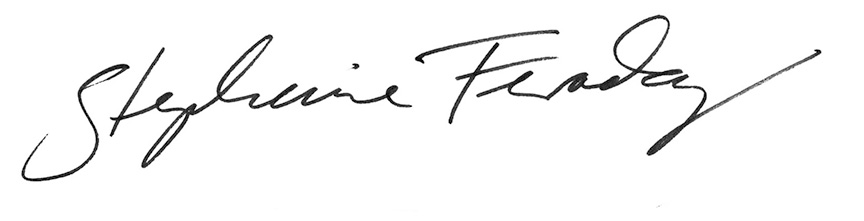
Our Partnerships Yield Innovative, Profitable, and Sustainable Products
Click below to see what to expect when partnering with aPriori:
Cost Estimation Accuracy
Real-Time Visibility
Achievable Sustainability Initiatives
Global Collaboration
Product Lifecycle Optimization
Enhanced Competitiveness
Fast and Significant ROI is Our Primary Objective
Our customers – ranging from aerospace and automotive to high-tech and industrial – realize a fast return on their digital transformation investments by partnering with our Customer Success and Expert Services teams to develop custom deployment plans aligned with their corporate business objectives.
Analyst firm Forrester recently interviewed four aPriori customers. Based on a three-year, risk-adjusted present value (PV) for customers, Forrester found that they gained a: