Video
The Price of Precision: How Tolerances Shape Cost and Manufacturability
Join the aPriori Product Management team to learn how aP Design’s latest capabilities add value to your everyday workflows. We will also share multiple customer case studies that show the effect that tolerances can have on both the cost and the manufacturability of your product design.
3 Key Takeaways:
1. Learn how tolerances are added in aP Design
2. Understand the importance of tolerances to cost
3. Determine the value of assessing cost during the design phase
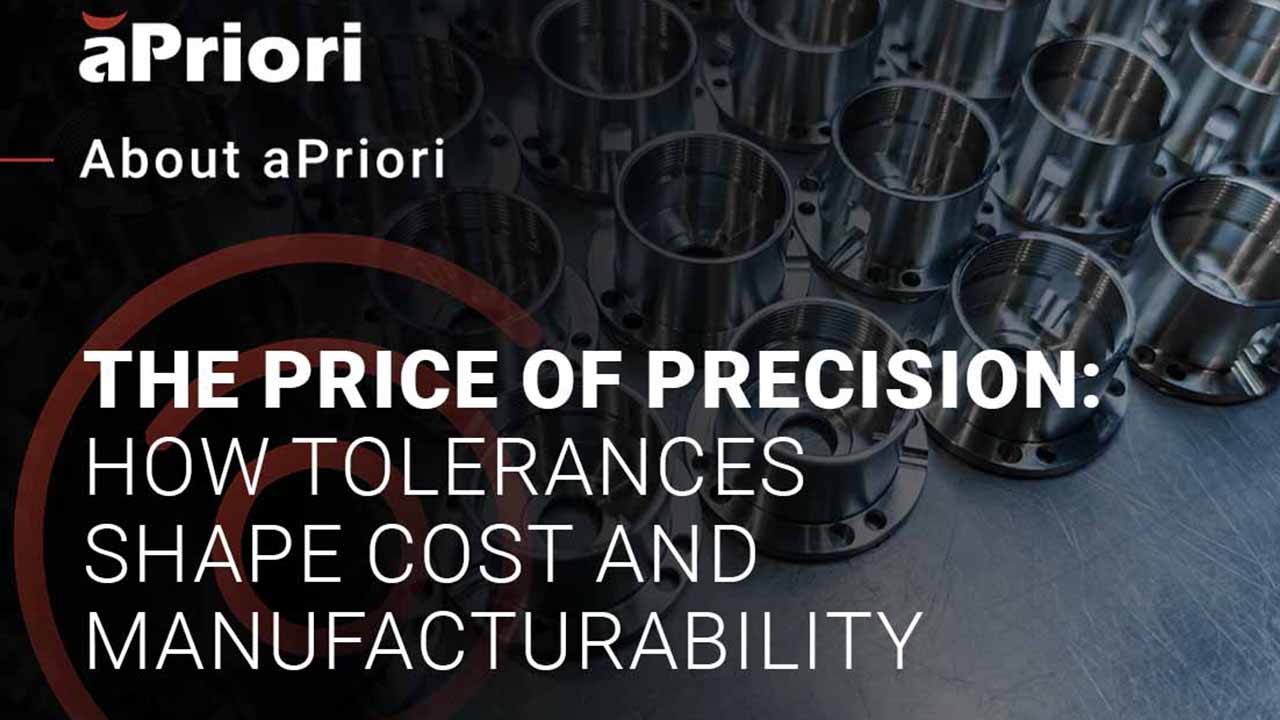
Transcript
Matthew Mullen: Welcome to this session. The title of this section is going to be The Price of Precision. So my name is Matthew Mullen. I am the Director of Cost Law Development for aPriori. I’ve been with the company for about seven years now and before that had a number of engineering roles within the aerospace manufacturing industry.
James Ferguson: My name is James Ferguson, and I’m the product manager for AP Design here at aPriori. And prior to this, I was an engineer manager at an automotive company working in body engineering.
MM: So today we’re going to explore three different areas. Firstly, we want to understand the importance of tolerances and how they impact the cost of manufacture; show the value of that understanding and the impact during the design phase; and then, finally, how tolerances are applied to scenarios within aPriori Pro and leverage the insights that are provided. So in Belfast, where James and I are from, we have three big manufacturing companies:
Tolerance Challenges
MM: A shipbuilder, an aircraft manufacturer, and a company that develops components for airspace and defense industry. In a place as small as Northern Ireland, you can imagine there’s quite a bit of rivalry between the engineers at these three sites arguing about who designs and builds the best components. One day, when I was working at the aircraft manufacturer, I overheard one of these heated discussions.
MM: The aircraft machinist was bragging that he could hold tolerances on his part to within five-thousands of an inch. The space and defense guy, not one to back down from a challenge, declared, “That’s child’s play. I can regularly make parts accurate to within plus or minus two-thousands of an inch.” And without missing a beat, the shipbuilder chimed in, “That’s all well and good, but we make our parts dead on.” And that, that’s part of the issue here, that a drawing, a CAD file, a computer model, represents a concept that is perfect. The manufacturing component is actually imperfect, and a major barrier in the journey from conceptual design through to tangible products is variation, and that variation can occur in the manufacturing products as well as the processes that are used to develop them. For designers of components, it’s vitally important to know the capability of the process that will be used to manufacture the particular product feature.
Bilateral Tolerance
MM: With this knowledge for each critical quality characteristic, an estimate of the number of defects that are likely to happen in the manufacturing this part can be made. The dimensional management is a process by which design, fabrication, and inspection of a product are systematically defined and monitored to meet predetermined dimensional quality goal. Ultimately, it’s an engineering process that is combined with a set of tools that make it possible to understand and design for in variation. If it’s done right, it’s going to improve first time quality, performance, service life of the component, and associated costs that go with that.
Geometric dimensioning and tolerancing is an international engineering drawing system that offers a standard way to specify 3D design dimensions and tolerances on an engineering drawing. It’s based on a set of universally accepted graphical language and published in national and international standards. Most importantly, it’s a framework which removes the ambiguity in the contract between the designer, the manufacturer, and the consumer of the product.
Why Tolerances Are Important
MM: Working with and applying tolerances in CAD models is critical for a robust design. As I mentioned previously, it plays an important part in a number of important roles. It ensures that the final product meets the quality standards that are required in service. It specifies the dimensions to ensure functional relationships with other components can be met, that the component can be physically manufactured, and it also provides the information that can be used to control the tooling and the assembly interfaces that help with fitment in later assembly stages. So a study conducted by the SME showed that 70% of manufacturers believe that tolerancing is the most important factor that affects costs within manufacturing. So how does it affect cost? Well, the answer is not merely to apply more tolerances or tighter tolerances. Tolerances not only drive quality, but they also drive the cost.
MM: And there’s a band here where applying appropriate tolerances to meet the functional requirements of the component facilitates the manufacturer of the component and the downstream assembly fitment. For example, looser tolerances allow for greater variation in the part dimensions, they simplify the manufacturing processes, they require less precise equipment and labor. This can often lead to faster manufacturing processes because there’s less emphasis on precision. It can reduce waste because parts with slight variations may be acceptable. And it requires less stringent quality control in terms of inspection and the associated cost of the tools. In order to do that.
Precise Machining or Manufacturing Processes
MM: There may be times when a tighter tolerance is required, but having the knowledge that this will typically require more precise machining or manufacturing processes which can increase production costs, more specialized equipment will be required for tighter tolerances, higher skill labor, higher tolerance tooling, you may need to slow down the machining feeds and speeds or the manufacturing process in order to ensure this accuracy, these can all increase cycle times as more attention, detail, or quality control is necessary. There may be more material wastage because parts that do not meet the stringent requirements may need to be scrapped or are reworked. And those tighter tolerances require more extensive inspection on quality control measures within the process.
MM: If we think about how tolerance might dictate the choice of manufacturing processes in available, we have to consider this along with a number of other decisions that are being made in the design stages. So, I’m going to use an example of cutting a piece of rope that is about 100 inches long. If I asked one of you to do this, it would be a relatively simple task. The experienced amongst us might even leave a few extra inches on the end just to avoid cutting the rope too short. But it’s a relatively straightforward process. Think about what you would do differently if the exact length of the rope had to be within plus or minus one inch of that 100-inch limit. How would you approach the task differently? Maybe measure twice, use the table to lay out the rope? What if I then disclosed that this was a piece of rope that was to be used in a high-tech application, and the length now needed to be 100 inches to within one tenth of an inch?
Lower Deviation
MM: How would that change your approach to this? We can add in additional factors here. So, if we want to scale this up into an industrial application and introduce more pieces of rope, maybe say we’re making 2,000 pieces, this again has another impact on our manufacturing choices and how we ensure this conformity to different manufacturing tolerances. As you can see in the chart on the left, there within the same process different operations can achieve varying levels of tolerance. The larger the IT number, the lower the tolerance class or the lower the accuracy. And the wider the allowable range, the less difficult the processing is. The IT grade refers to an international tolerance grade for international processes, which are defined in ISO. But this is a balancing act.
MM: It’s a trade-off between costs incurred now and potential costs that can be incurred downstream. It’s not the same for all parts. The impact of tolerance on manufacturing costs was found to be greater for smaller parts than larger parts. It’s found that the impact on manufacturing costs was greater for parts that were made of materials that are difficult to machine, such as hardened steels or titanium. The impact of tolerance on manufacturing costs was found to be greater for parts that were made using complex manufacturing processes. These were all the results of a study from the University of Michigan that showed that a 10% reduction in tolerance could lead to a 20% reduction in manufacturing costs. But as you can see in the graph on the right, there is an optimum here. As we widen those tolerance bounds, as we relax the accuracy that needs to be achieved, it has knock-on consequences downstream.
MM: The study concluded that manufacturers can significantly reduce the costs by carefully considering the required tolerances for each feature of their product. Tighter tolerances should only be used when we have an absolute necessity to do so. It also found that the impact of tolerance on manufacturing costs can be reduced by using design for manufacturability principles. These principles are used to design products that are easy to manufacture and assemble. For example, DFN principles can be used to design parts with tolerances that are grouped together and can reduce the number of manufacturing operations required. So, finally for me then, before I hand over to James, to summarize the importance of geometric tolerancing.
Geometric Tolerance
MM: Geometric tolerancing is an essential tool within the designer’s toolbox for creating robust designs that are capable of being produced and assembled reliably. By identifying capable production processes preventing later assembly issues and minimizing scrap and rework, by specifying the right geometric tolerance, can help companies save time and money. By ensuring components conform to these requirements, future assembly issues can be avoided to ensure that all parts fit together correctly. For example, a geometric tolerance on the diameter of a hole can help to ensure the shaft will fit into the hole smoothly without binding. With the same application of tolerance, we can also have that same shaft and same hole fit together with an interference fit just by specifying different tolerances. So, I’m going to hand over to James now to allow him to talk through the importance of identifying these design stages and also how we apply it within AP design.
JF: Thanks, Matt. So Matt spoke about the tolerance and why they’re important, and I want to take a little bit of time to talk about what happens when we don’t apply tolerances and then move on to look at reviewing different ways, we can apply tolerances and how APD might be able to help you. Imagine, if you will, a world without engineering tolerances. It’s pretty easy to do, just imagine a world where pretty much nothing fits together. If we take these simple LEGO blocks, for example, if all we do is apply to the nearest millimeter the measurements then we’re setting ourselves up for a world where a percentage of blocks won’t fit, a percentage of blocks will be too tight, a percentage of blocks will be too small, a percentage of blocks will be too tall, and essentially nothing will work together. It’ll make it impossible for customers to build LEGO assemblies, let alone provide LEGO kits.
JF: Luckily for us, that’s not the case, and LEGO spends months upon months defining tolerances for even the simplest blocks, taking measurements, conducting FEA and MOFO studies, theorizing and optimizing every last measurement to the possible fit. And it’s due to this due diligence and the effort that allows these small bricks to be used to build complex LEGO assemblies, and it’s the same principles of well-considered, well-applied design that underpins and enables the design of much more complex parts, systems, and assemblies. Higher tolerances specified. Tolerances are best applied during the design phase of a product development, and they’re typically applied in three ways.
Targeted Tolerance Application
JF: First, and my favorite way, is through feature targeted tolerance application. The first is my favorite way, through feature specific targeted tolerance application applied with careful consideration to 2D and 3D drawings. Then, through generic policy, whereby in the absence of adding specific tolerances we can assume generic band tolerances correlating to the product’s overall size, dimensions, and manufacturing route are applied. And then, sadly, we have the third way, which is the most upsetting way of all, and it’s badly or not at all. Not applying tolerances leaves room for interpretation. Different machines have different tolerances, and not specifying the model can result in poorly controlled final products causing fitment and finish issues. I’d also like to take this opportunity to bust the myth that lots of tolerance is good tolerance. That is not the case.
MM: I’ll now step through a really simple scenario where we can visualize the effect of tolerance and the effect it might have. Taking one of our favorite parts, we can walk through what happens when we first apply no tolerance, then the appropriate tolerance, and finally excessive tolerance, and understand the impact. Firstly, no tolerance. Let’s call this the baseline for cost and cycle time. The part appears to be producible, but we can’t ignore the effect the lack of the extra dimensional control is going to have. It will be unpredictable and ill-fitting when paired with other mating parts, and it will most likely incur rework or rejection. Then when costed with the appropriate tolerance, we can see that we can maintain production with the same machine as our first routing, albeit with a few minor corrections. A slightly higher cycle time resulting in a small increase to the cost, but delivering a well-controlled, accurate part, ensuring repeatable production and assembly, is a price that I’d be willing to pay. And then lastly, let’s go wild. Let’s apply all the tolerances we can think of.
JF: This tips the scales and incurs a wrath of additional specialized tooling and dramatic cost and cycle time increases and still results in high scrap and excessive costs. Arguably, it’s just as bad as applying no tolerances at all. The key takeaway here is that when we’re careful and considerate in our tolerance application the impact to our cost and cycle time doesn’t need to be huge. In this case, with less than 1% increase when compared to no tolerance, it’s going to result in a much more efficient and exponential return in costs in terms of cost avoidance. Tolerance really is a bit of an art as much of it is a science. aPriori Design has DFM guidance built in specifically aimed at alerting you to issues caused or related to tolerance; however, I’d also like to take the opportunity to walk through some of the key features introduced this year that I feel can really help you when it comes to adding, editing, or relaxing tolerances today.
Different Tolerances
JF: Obviously key to what we’ve been speaking about today, aP Design lets you add and edit tolerances directly in the application letting you choose features and faces to target and doing some of the mental math like filtering out unsuitable tolerance types based on your features selected. aP Design also supports tolerances being imported directly from CAD through PMI and the application of a CAD tolerance policy. Next, as you add and edit the tolerances in aP Design, we provide you with detailed cost, carbon, and DFM feedback to let you understand how your decisions will ultimately affect your design.
JF: And as of this month, and I must admit this is one of my favorite features, aP Design will let you see and track the progress you make as you iterate through design revisions and allow you to plot on a biaxial graph a combination of over 12 outputs, including for example cycle time versus cost, total investment, or carbon. I think this is one of the best views to understand at a true engineering level, the impact of our decisions on the design and how it can shape the journey that our partner assembly undergoes during its design refinement phase. And finally, as of September, aP Design lets you build and save comparisons, showing a customizable and detailed breakdown of how each scenario stacks up against each other in order to highlight or justify final design selection. All these tools and many more form the backbone of aP Design built and reformed by design and manufacturing engineers to be used by design engineers to help make your products the best they can be.
Thank you very much.