Video
How to Automate Your Design for Manufacturability Workflows
Is it possible to automate your design for manufacturability (DFM) initiatives? The answer is yes.
This presentation gives you a complete overview of using automated workflows to provide DFM insights and guidance at the early stages of the design process. You’ll learn how to optimize components that are cost-effective and manufacturing friendly.
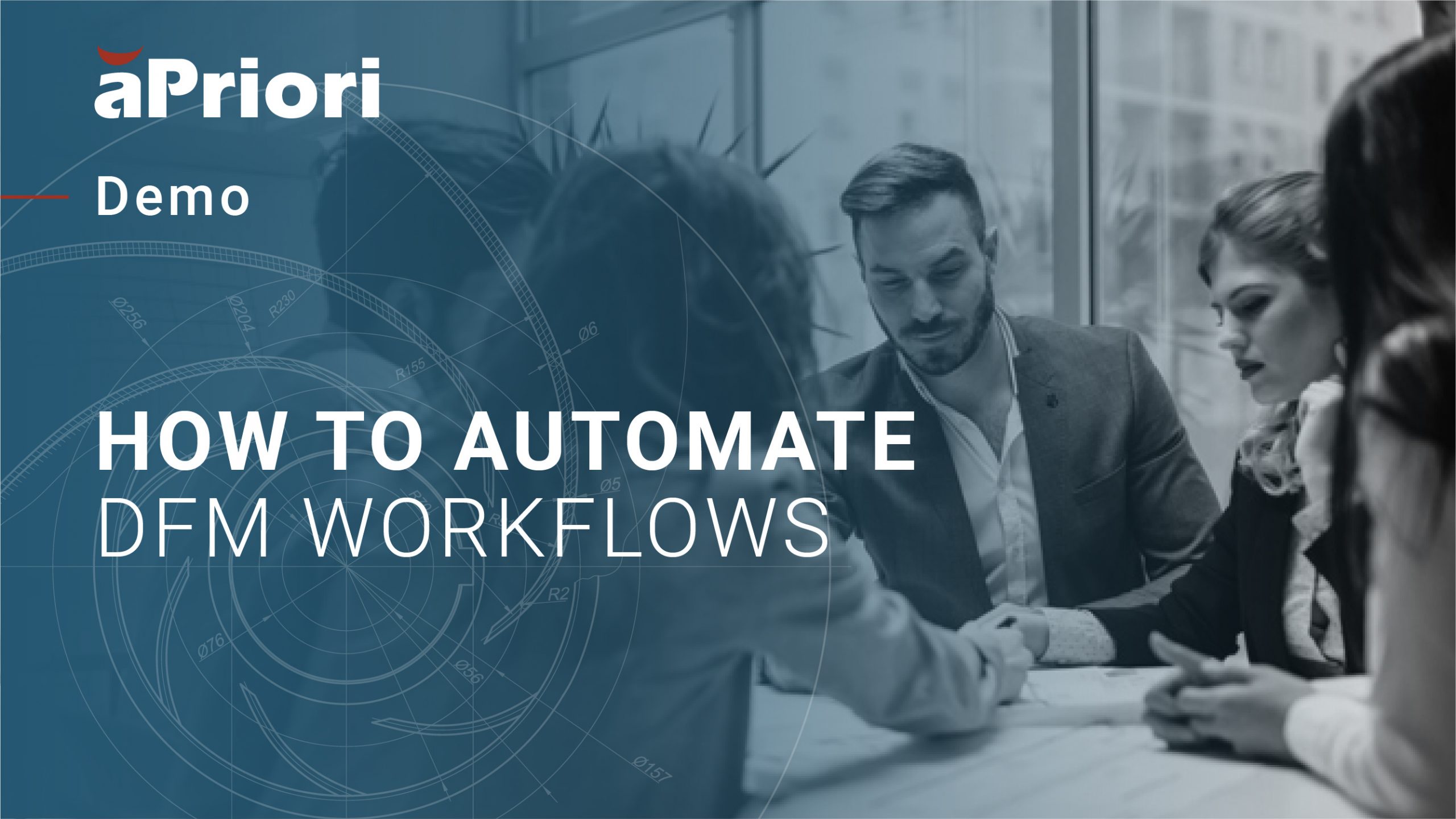
Transcript
Christopher da Rosa: Hello, everyone, and welcome to Next-Generation Automation for Manufacturability for Engineers. My name is Christopher da Rosa, and I am an Application Engineer at aPriori. This session will consist of a 10- to 15-minute demonstration, but before we begin, I just have a few housekeeping notes. If you have any questions after you view this demo, I will be live in the meeting room from 2:00-5:00 PM Eastern time, so feel free to join by clicking the join trade show button in this virtual booth to connect and have your questions answered. If that time block doesn’t work for you or you prefer to meet one-on-one, you can also schedule time with me via the meeting scheduler on the event website near the chat panel and choose people. In this case, select my name, Christopher da Rosa, and schedule a meeting with me. Alternatively, you can use the leave-your-card button on the virtual booth page to have somebody reach out to you. We have also uploaded a PDF of today’s presentation, plus additional resources, which you can access in the files panel. So, with all of that, let’s begin.
Again, welcome to aPriori’s 2021 Cost Insight Conference. Today’s session is Next-Generation Automation and Design for Manufacturability for Engineers. Before we jump into the demo, I just wanted to share a quick little bit about myself. My name is Christopher da Rosa, Application Engineer at aPriori. Previous to joining aPriori, I started out as a machinist at the young age of 17 and went on to get my bachelor’s degree in mechanical engineering at the University of Buffalo. I’ve worked for 15 plus years as a mechanical design engineer, CAD, and PLM administrator and manager, serving many industries, such as aerospace, DOD, pumps and compressor systems, and custom automation manufacturing equipment.
Streamline Product Manufacturing Workflows With aPriori’s Real-Time Insights
A high-level note on today’s demonstration: This will be an overview of how aPriori’s automated solution Cost Insight Generate, also known as CIG, can support design engineers and their new product initiatives and provide design for manufacturability insights and guidance at the early stages of the design process. This will allow engineers to optimize cost-effective and manufacturable-friendly components. And so it all starts with the design engineer, who spends most of their days working in their CAD environment. At some stage in the design process, the engineer is satisfied with their initial design and will check the part or assembly into the PLM system. Through Cost Insight Generate’s automation, an analysis can be initiated at any defined trigger, such as a component check-in or workflow state change or milestone.
Whatever that trigger may be, the automation is underway, analyzing all the parts initiated under the workflow. From here, all the relevant data and reports for should cost and manufacturability are written back into the PLM system. They are also available in the aPriori environment for others to consume. As this automated action is completed, an email notification will be sent out to all relevant parties, highlighting the collection of components that were analyzed. From here, a design engineer can use this automated email as the first level of guidance to understand which components may require further attention from a design for manufacturability standpoint.
Gain Actionable Notifications to Improve Supply Chain and Product Design Decisions
Reports and hyperlinks for each component are available in this email notification, allowing the engineer to quickly access the analysis and insights to investigate further. Okay, so I’m going to start this demonstration at the fourth stage shown in this slide and work through how we arrived at this point. Here is the automated email of a DFM part summary report I received, which was automatically generated with CIG. At the top of the email are the attached PDF reports for each of the components analyzed. It’s also important to note that these reports also get attached to your PLM database along with the respective data, such as your should cost and DFM risk rating. As we open the part summary report, we can view all the resultant data provided by the automated analysis. You’ll see a complete itemized breakup of the part with details such as manufacturing process routings, volume in production life, cost details, and raw material information such as rough mass and material utilization.
On the next page of the report, we can view any design-to-cost metrics, highlighting potential cost drivers associated with each feature of the component. And further information like manufacturing issues, slow machining operations or tolerances that drive specialized operations, or any additional machining set-ups to provide a great overview for each part.
Looking at the rest of the content of the email, we will see a summary report list of each component analyzed. We quickly identify the part number, manufacturing process group, DFM risk rating, and the aPriori should cost for each part. As we look down at the list, we can very clearly see that we have a couple of parts that were flagged as potential outliers in regard to the DFM risk rating. Indicated with a high-risk score shown in red, these are the parts we will likely look to address first. Using the part number hyperlink, we can open the component in aPriori’s cloud solution, Cost Insight Design, to investigate further. Here, we can see the initial inputs to analyze, such as the manufacturing process and virtual production environment, also known as the digital factory, and volumes and material. We’ll see all the resultant data from the automated analysis and understand the process routing on how this component will be manufactured. Along with the should cost, which were yielded for this process. We can begin to explore the results and look at things like the material and utilization percentage. Here we see we have a very low percentage of fairly expensive material. So, perhaps we should mainly explore other production processes like castings, which we can do very easily by creating a new scenario.
However, our main focus right now is the design guidance window. This is where we were initially flagged to the high DFM risk rating. The first warning is showing a side milling length-to-diameter ratio issue due to the small radius we find in these pockets. If I wanna understand more details about this problem, I can click on the insights icon to capture a deeper explanation of the problem and solution.
Next, we see that a particular tolerance is driving a special finished operation, which is adding extra costs to the component. aPriori will show you the tolerance location and offer the basic machining element within that threshold. If you were able to loosen this tolerance, we could do away with this reaming operation and save some money on this component. This is, of course, maybe purely due to design intent, in which case we can look to ignore this warning. Other feedback we see is other cost-driving information, such as slow machining operations, flagging us to areas or bottlenecks in the model that are at a higher cycle time. In this case, we have this contoured surface and these contoured milled corners that are all contributing to the slow machining operations and increasing our cycle time. If we wanna dive even deeper, we can go into this investigation tip to get a more visual depiction of this impact. We can even generate a nice heat map on cycle times for each feature.
Of course, there may, again, be design intent for these types of features, but should you be able to make any design changes based on this type of feedback, you’re doing it at the right time in the design process and ultimately working towards an optimal solution. Under this results window, we can also capture a nice breakdown of the cost. And of course, we can see that the material and labor account for over 60%, so anything we could do from a design standpoint to make this part more manufacturable-friendly will help to lower our costs. So, let’s take all this feedback and jump into our CAD model to make some design changes based on the guidance that aPriori provided. For this CAD model, I’m working in NX, which is also connected to our team center PLM. I’ll look to address some of the design for manufacturability warnings that I was being flagged for. I’ll start by increasing the radius inside these pockets to satisfy our side milling length-to-diameter ratio warning. This will allow for a larger end mill to machine out these pockets. And at the same time, this should also do away with our contoured milled corners issue since we will no longer have that blended radius in each corner of the pockets, which was indicated by a slow machining operation.
I’ll also make a subtle change to this contoured surface, while from a design standpoint, I will need to maintain the contour; I can do away with the filleted edge around it to save on some cycle time. A simple deburr call-out of my drawing will satisfy any potential sharp edge issues. From here, I can go about this two ways: I could check this part back into the PLM and wait for the results via the automated email notification, which is where we first started this demonstration, or I can utilize the CAD plugin, which will launch the updated CAD model into cost insight design. For the demo’s sake, we’ll use the plugin to initiate the revised analysis. Let’s go ahead and verify that our changes have satisfied our initial warnings. As we can see, we are now at a low DFM risk rating from the initial high rating we received. When compared to our initial analysis, we can quantify the impact these simple design changes had on the component. Again, we brought down our DFM risk rating from high to low. Most notably, as we look at our process tab, we can see that we cut down our machine cycle time by over 45%, which yielded significant savings on our component, down from $17.55 to $12.27, a 30% net savings on this part.
Powerful Workflow Automation for Collaborative and Informed Business Processes
So, just to recap where this all started, I designed a collection of components in CAD by checking in the components to the PLM. An automated analysis was triggered in aPriori, and I received an email notification with a completed summary report. Inside this report it flagged me to this particular component, having shown a high DFM risk rating. I then quickly navigated to this part via the hyperlink and viewed it inside Cost Insight Design. Using aPriori’s design guidance feedback, I jumped back into my CAD software. I made some simple changes to this part, which had a significant impact on this component and the project moving forward. I went from avoiding potentially costly engineering change orders to a fully optimized, manufacturable-efficient component at the earliest stages of the design process. Just to close the loop on this automated manufacturing workflow, I want to quickly give a look into our PLM environment and show the relationship between the data being written back into the PLM. In this case, we’re showing our team center database dashboard. Here, we could see the inputs that drove the automation in our sandbox environment. We defined the check-in action to trigger the automated analysis. As we jump to the outputs tab, we can see that information we configured to write back to our components. These are the data points we felt were most valuable in our environment. Information like DFM risk rating, fully burdened piece part cost, and cycle times, amongst other data.
All this data is now available in the PLM environment and attached throughout the life cycle of each component. It also lives in aPriori for further consumption and collaboration among other team members in manufacturing companies, such as project managers and cost engineers, to take advantage of the other functionalities that aPriori solutions cover. This concludes the demonstration. Thank you for watching this session. If you have any questions at this time, please feel free to join the Live Meeting within this booth by clicking the “join trade show” button in the virtual booth. You can also download additional resources on this topic, schedule a time to meet with me one-on-one, and do other demonstrations on the main product demo page. Thanks again, and have a great day.